Well-Rounded Processes in Edging Production
More Efficient Methods for Producing Metal Profiles
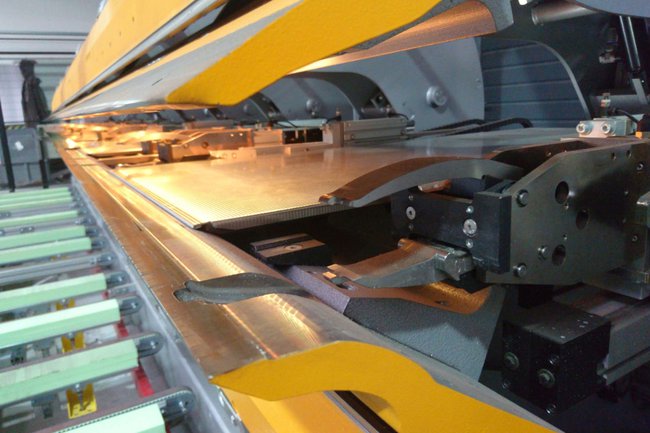
In a collaborative project, the St. Pölten University of Applied Sciences and its partner companies have developed a method to improve planning in the production of metal profiles.
The goal is to make the production more efficient and create less waste in test runs. The data management is to make companies fit for Industry 4.0.
Sharing Experiences, Freeing Staff
The project “WiKant – Wissensbasierte Kantteilfertigung” (Knowledge-Based Edging Production) has developed a data and knowledge management prototype that helps companies find out prior to a test run on the machine whether a planned metal profile can be produced on the existing bending machine or not. In this way, production facilities save time and raw materials by reducing test runs, defective parts and samples.
“As the results are saved, the system combines the experiences of many production workers and the machines are equipped with past knowledge, as it were. This helps save intensive training and long learning periods on the machines, thus enabling the employees to carry out more demanding tasks such as quality assurance and production planning”, explains Thomas Moser, head of the research group Digital Technologies at the St. Pölten.
Machines Fit for Industry 4.0
This innovation makes bending machines fit for the requirements of Industry 4.0. “The feasibility analyses are currently the biggest hurdle for an interconnected and automated production using bending machines. Even with the most intensive process optimisation, the problem remains that every single part has to be tested by the production staff”, says Moser.
At the moment, there is no possibility to reliably assess similar recurrent parts without a manual test because the result of the bending process may differ from known profiles in case of even the slightest deviation. The research project headed by the St. Pölten UAS uses machine learning processes for the new analysis methods. The partner companies in the project were Metaflex Kanttechnik GmbH and nuIT.
Sharing Knowledge
The project team designed a knowledge-based and rule-driven system and developed a prototype that was tested on a modern production machine of the company Metaflex Kanttechnik GmbH. The challenge now is to harness the experiences gained for other machines, as innumerable production machines from different manufacturers and construction years are used in the market.
“We are planning to connect new customers with their different production machines to the system in future, so that production facilities can profit from each other’s wealth of experience. While the companies do disclose their knowledge, they can profit from the knowledge of all others, which saves them time and resources”, emphasises Moser.
For this reason, the knowledge-based system developed in the project is to be applied on a larger scale in the near future. According to Moser, the system can also be applied in other branches of the industry if it is adapted accordingly. Companies active in edging production or other sectors looking to evaluate manufacturability tests using machine learning can contact the project team at any time by sending an e-mail to thomas.moser@fhstp.ac.at.
Project “WiKant – Wissensbasierte Kantteilfertigung“
The project WiKant was subsidised by the province of Lower Austria within the framework of the FTI research, technology and innovation programme Lower Austria.
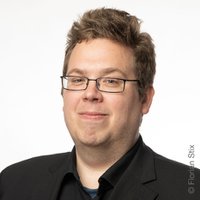
FH-Prof. Dr. Thomas Moser
Head of Research InstituteInstitute of Creative\Media/Technologies Deputy Academic Director Smart Engineering (BA) Senior Researcher Industry 4.0 Smart Engineering (BA) Department of Media and Digital Technologies