Breadcrumbs
- Smart Engineering of Production Technologies and Processes
- Projekte
- Wertstromanalyse Rapid Response Production (RRP)
Wertstromanalyse Rapid Response Production (RRP)
Wertstromanalyse zur Ursachenfindung einer unerwünscht hohen Zahl an Items im Backlog.
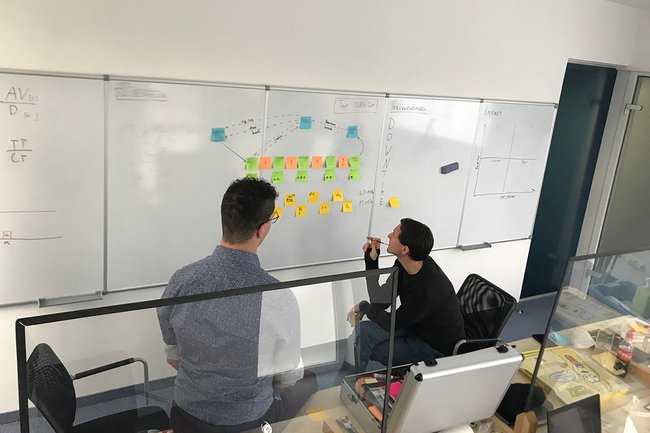
Hintergrund
In der Rapid Response Production am Standort Pasching der Global Life Science Solutions Austria GmbH & Co KG werden pharmazeutische Produkte mit niedrigerem Qualitätsstandard und damit einer deutlich geringeren Durchlaufzeit als in der regulären Produktion hergestellt. Diese Produkte dienen nicht der Herstellung von Medikamenten, sondern werden meist zur Entwicklung neuer Produkte herangezogen, die dann in größerem Maßstab und nach den entsprechenden Standards in der regulären Produktion hergestellt werden können.
Problemstellung
Mit Stand Dezember 2021 ist man mit der Produktion von insgesamt 25 Chargen, die eigentlich schon ausgeliefert hätten werden sollen, im Rückstand. Der Trend ist steigend. Das Limit für diesen Backlog sind eigentlich 5 Chargen.
Die Problemstellung und der dokumentierte Lösungsansatz | Copyright: Stefan Hofbauer
Stefan Hofbauer widmete sich in seinem dualen Projekt im dritten Semester diesem Problem. Mittels Wertstromanalyse des Prozesses sollten Verschwendungen und Potentiale identifiziert und mögliche Maßnahmen zur Behebung definiert werden.
Projektablauf & Ergebnisse
Um der seit längerem auftretenden Verspätung von Produktionen und dem sich dadurch aufbauenden Backlog entgegenzuwirken, wurde eine Wertstromanalyse des Prozesses durchgeführt. Dabei konnten mehrere Problemstellen, wie zum Beispiel das Fehlen von standardisierten Prozessen für die Vorbereitung der Produktion, identifiziert werden.
Nachdem die Probleme erkannt waren, folgte ein Brainstorming, um Lösungsansätze zu sammeln. Die Ideen wurden anschließend mit einer Eisenhower-Matrix bewertet und jene Vorschläge, die einen hohen Einfluss auf die Durchlaufzeit haben, zur Umsetzung ausgewählt.
Bei der Ausarbeitung des Wertstroms und der Impact Matrix | Copyright: Stefan Hofbauer
"Es werden standardisierte Prozesse zur Vorbereitung einer Produktion eingeführt, sodass auch Lehrlinge und Mitarbeiter*innen, die in der Abteilung nur aushelfen, selbstständig mit der Arbeit beginnen können. Außerdem wird derzeit ein Teil der Abfüllung automatisiert, der eine*n Mitarbeiter*in komplett bindet, aber nur wenig auslastet. Diese*r Mitarbeiter*in kann zukünftig bereits mit Vor- oder Nachbereitungen beginnen, während eine Charge noch produziert wird. Auch in unseren Computersystemen konnte Potential zur Verbesserung identifiziert werden, indem eine überflüssige Freigabe entfernt wurde", erklärt Stefan Hofbauer die ausgewählten Maßnahmen genauer.
Insgesamt kann die Durchlaufzeit der Produktion dadurch von ungefähr 15 Stunden pro Charge auf 12,5 Stunden gesenkt und damit der Kundenbedarf gedeckt werden. Der Backlog konnte ebenfalls reduziert werden und beträgt statt 25 (Stand Dezember 2021) nur noch 3 (Stand Mai 2022) Chargen.